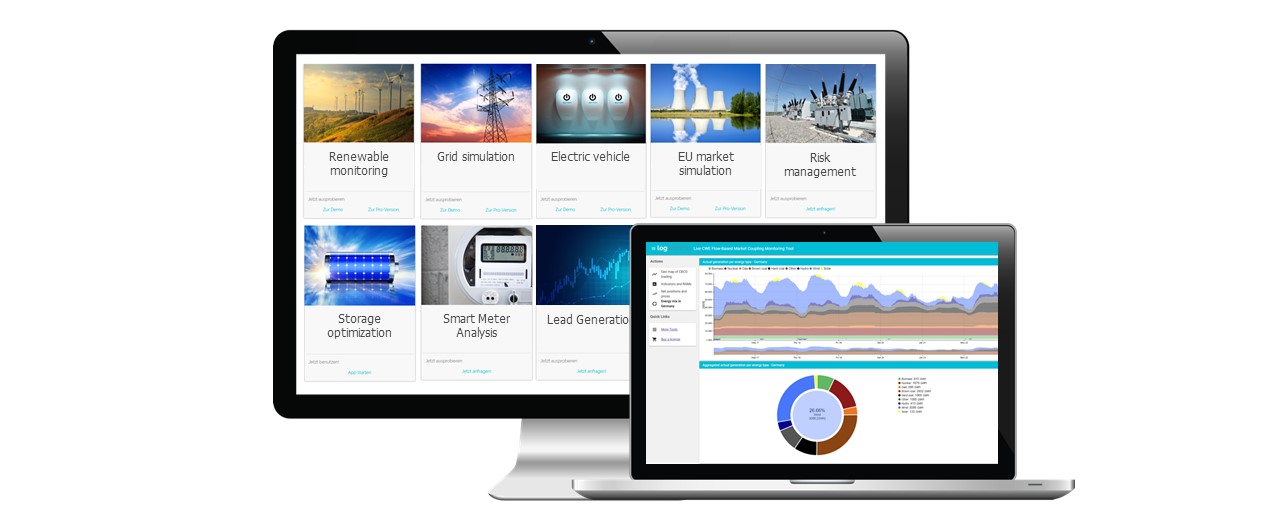
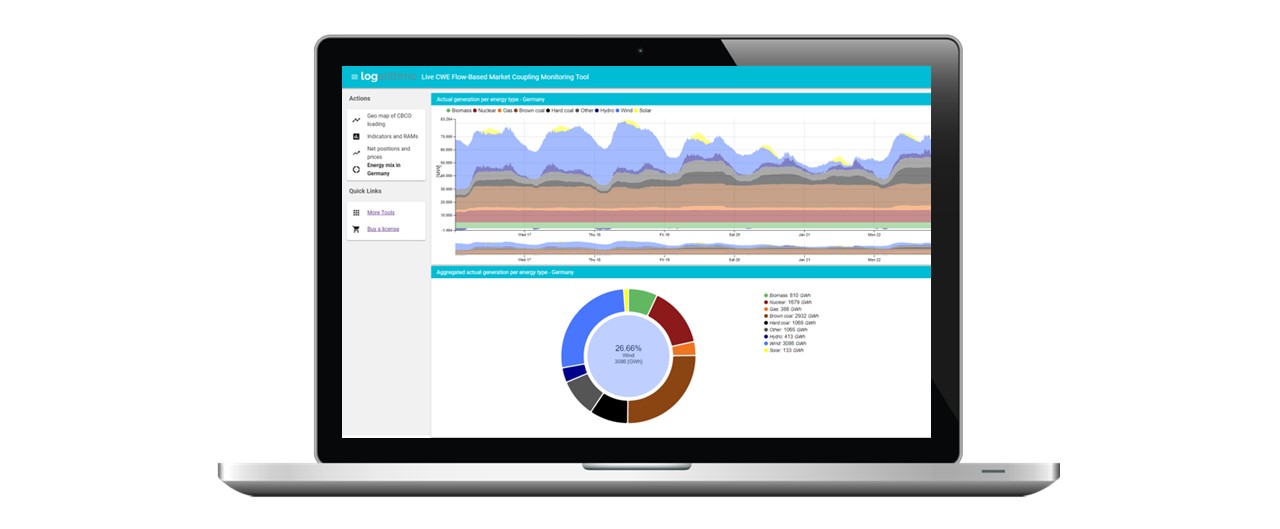
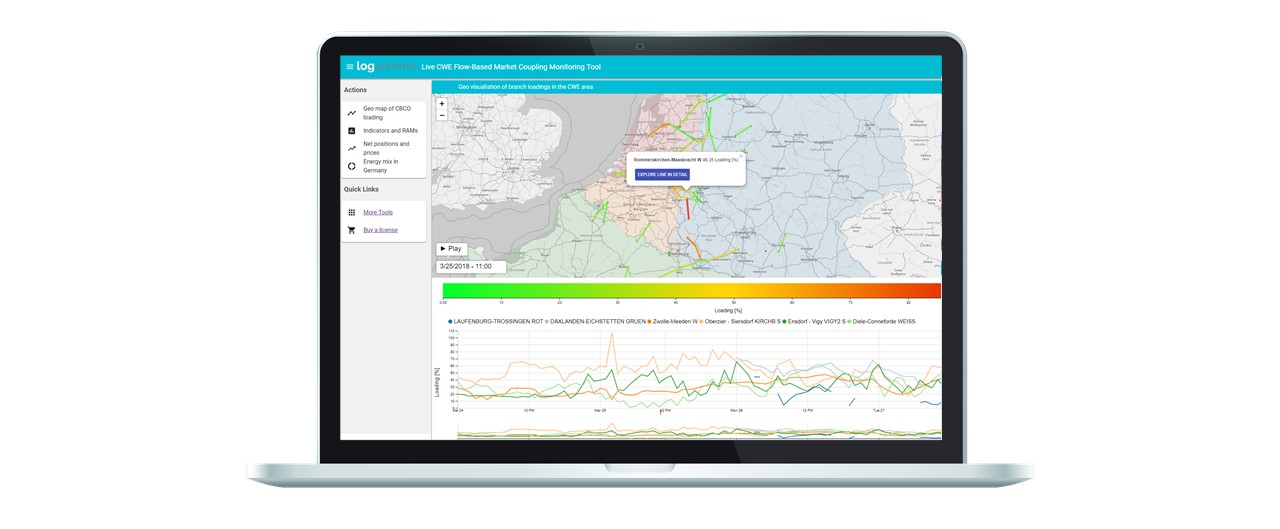
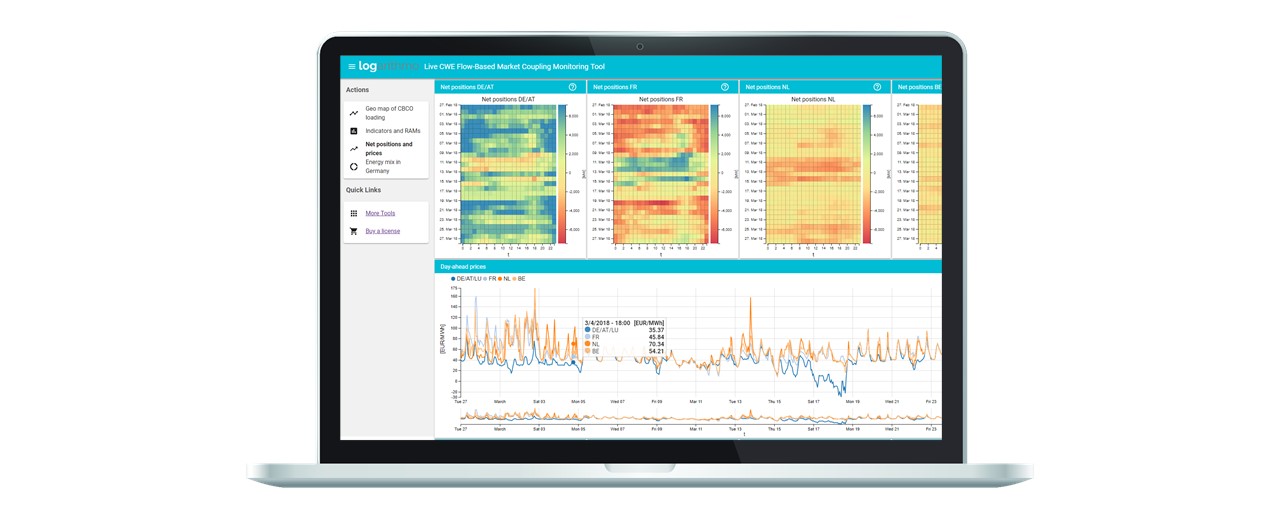
The planning goals in the area of production vary from industry to industry. While in the process industry the plants are often very expensive and are used to the best possible capacity, in other industries the materials are expensive and are planned with higher capacity buffers and produced according to orders. These target values are taken into account, for example, in production planning and control.
The different target values in production planning, capacity restrictions at different locations or sales uncertainties can be mapped in a targeted manner through optimization and simulation. By using sensors or the installation of additional sensors, predictions about the probability of failure can also be made, e.g. by using models based on artificial intelligence. In combination with the industry knowledge from the energy sector, logarithmo also offers benchmarking and potential analyses in the field of energy efficiency.
Monitoring of the operating status
Monitoring of reliability, bottlenecks or energy efficiency.
Capacity scheduling
Ex-post analyses for internal material flow planning to support optimization measures.
Planning of warehouse stocks
Optimisation of stock levels to ensure a smooth overall process.
Application example - Production
A globally active industrial group aims to optimize its production in terms of return on invested capital (ROIC) and to prioritize projects that support this goal.
In one project, the various production lines at the sites were first mapped using an optimization model, and in the second step the impact of the projects was estimated. The result was a prioritisation of the planned individual projects against the background of the individual objectives for optimising the ROIC.
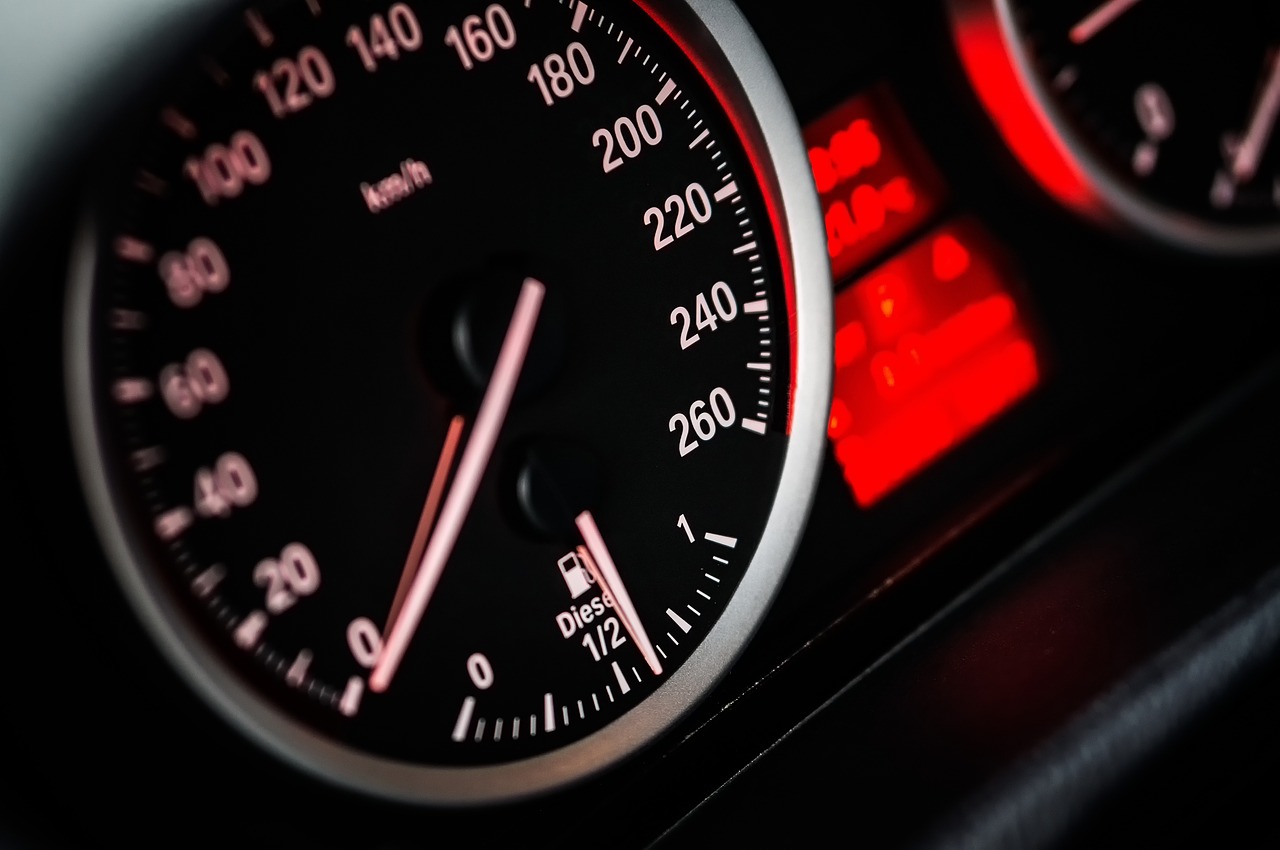
Our portfolio
Manufacturing logistics
Visualization of internal transports, e.g. in the form of a heatmap. Uncovering potentials.
Coordination of production processes and planning of warehouse stocks to ensure a smooth overall process.
Production scheduling
Creation of individual simulation and optimization models with the aid of an existing toolkit. This enables analyses in the global supply chain context.
Analysis of the current production processes with regard to throughput times, failure probabilities or quality. Support in planning capacity expansions.
Monitoring & Forecasting
Monitoring of the current system status using web applications that can be called via the browser or mobile device. Early alerting in case of deviations from the TARGET process.
Load profile analyses to uncover potential energy savings. Additional analyses, e.g. to save grid charges for investments in energy storage.
Use of existing sensor data to point out machine failures at an early stage (e.g. through models based on artificial intelligence).